浅谈数控铣床几种对刀方法的分析比较
1、概述
数控铣床是在传统铣床基础上发展起来的一种新型数控装备,与传统铣床相比,数控铣床的加工工艺基本不变,结构也基本相似。但是数控铣床因采用数控技术,因而能加工轮廓形状比较复杂的零件,相比传统铣床具有零件加工适应性强的特点,比如可以加工用数学模型描述的复杂曲线零件以及三维空间曲面类零件;还具备在加工一次装夹定位后可以进行多道工序加工零件的功能;数控铣床加工精度高,数控装置的脉冲当量一般为0.001mm,生产自动化程度高,不但可以减轻操作者的劳动强度,还可有效避免了操作人员的操作失误;数控铣床一般不需要使用专用夹具,在更换加工工件时只需调整数控装置中的加工程序、装夹工具和调整刀具数据,因此,数控铣床可以使工作效率得到明显提高。
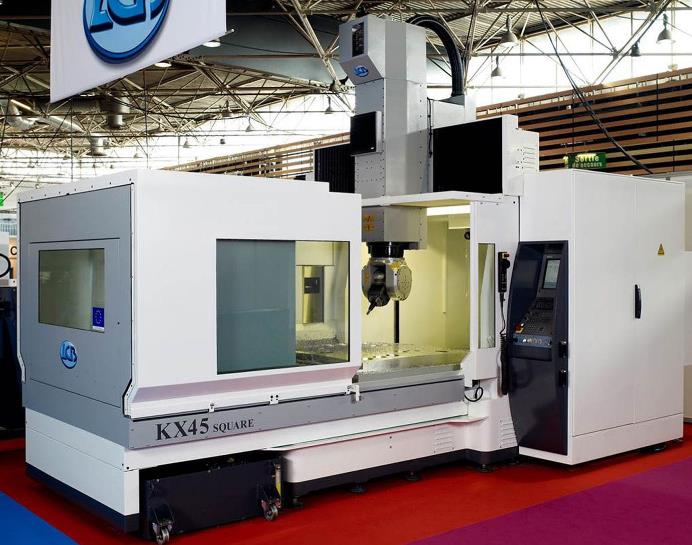
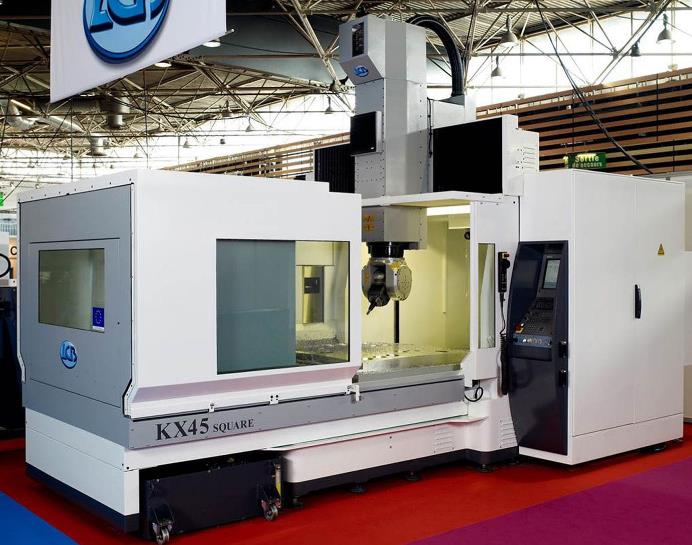
2、数控铣床对刀的重要性
数控铣床分为带刀库和不带刀库两大类,其中带刀库的数控铣床又称为加工中心。选用数控铣床刀具时,要根据被加工零件的几何形状、材料、表面质量要求、切削性能及加工余量等选择刚性好、耐用度高的刀具。铣刀的角度有前角、后角、主偏角、副偏角、刃倾角等,为满足不同的加工需要,有多种角度组合型式。对于数控铣床加工而言,其加工步骤主要为工艺分析、数学计算、编程及模拟、对刀、试切、正式加工等环节。其中,保证数控铣床加工质量的一项重要环节就是对刀,这是由于数控铣床本身的加工过程是按照编制程序进行控制的,只有建立正确合理的坐标系,才能保证刀具运动轨迹的合理性,进而保证加工质量。数控铣床坐标系分为机床坐标系和机械坐标系两种,其中机床坐标系是以机床参考点作为坐标原点建立的坐标系,而机械坐标值才是判断刀具位置的重要依据。对于数控铣床来说,由于工件原点是一个“动”点,只有确定工件原点的机械坐标值才能够准确地将编制程序运用到数控铣床加工之中,而想要准确地确定工件原点的机械坐标值就必须通过对刀来实现。
3、数控铣床对刀前的准备工作
3.1对刀点的确定
对刀点是工件在机床上定位装夹后,用于确定工件坐标系在机床坐标系中位置的基准点。对刀点的准确性是保证数控铣床加工精度的重要前提,因此对刀点的确定十分重要。“对刀点”又被称为“起刀点”和“程序起点”,其确定原则一般如下:(1)对刀点要有利于程序编程;(2)对刀点位置需容易被查看,进而方便机械加工;(3)对刀点位置需容易被检验,进而便于提高工件的加工精度;(4)在一般情况下,对刀点采用的均是工件坐标系的原点。
3.2换刀点的确定
在数控铣床加工过程中难免遇到多刀加工,无论是自动换刀还是手动换刀,都需要确定换刀点的位置。因此,确定换刀点对于数控铣床多刀加工时的精度掌握十分重要。一般情况下,换刀点确定是以不允许碰伤刀具、夹具和工件为原则,换刀点在加工工件的轮廓外,并留有一定的安全空间。
4、卧式数控铣床多工位加工中的对刀问题
对于卧式数控铣床(设工作台沿X向、Y向移动,主轴沿Z向移动),当主轴和工作台分别回零后,工作台回转中心将与机床参考点在水平面内的投影重合。此时工作台回转中心到主轴轴线与主轴前端面的交点的距离为XC、YC;机床坐标系下显示的坐标值此时为零,当主轴或工作台移动后,机床坐标系下所显示的X、Y值就是工作台回转中心相对机床参考点的坐标值,主轴中心相对机床原点的Z坐标值。在确定的工位,移动主轴(沿Z向移动)和工作台(沿X、Y向移动),使所选的工件原点在X向、Y向与主轴轴线重合,在Z向与主轴前端面重合,即刀位点与工件原点重合,这时工作台回转中心在机床坐标系中的坐标值,即为该工位时工件坐标系原点在机床坐标系中的坐标值。将此值输入到零点偏置寄存器相应位置,就可使用G54-G59指令建立工件坐标系。若使用G92指令建立工件坐标系,则刀位点也为主轴轴线与主轴前端面的交点,主轴和工作台的起始位置(程序起点)都在零点,则输入到零点偏置寄存器的值的负值即为G92指令后的X、Y、Z坐标值。
5、数控铣床几种对刀方法的分析比较
数控铣床加工时,对刀一般以机床主轴轴线与刀具端面的交点为刀位点。因此,无论采用何种工具对刀,目的都是为了使机床主轴轴线与刀具端面的交点与对刀点重合。
5.1对刀点为圆柱孔的中心线
5.1.1采用千分表对刀。该种操作方法比较麻烦,效率较低,但对刀精度较高,对被测孔的精度要求较高,该方法适用于经过铰或镗加工的孔,对于粗加工后的孔不宜采用该方法。
5.1.2采用寻边器对刀。光电式寻边器一般由柄部和触头组成,两者之间存有一个固定的电位差。当触头装在机床主轴上时,工作台上的工件与触头电位相同,当触头与工件表面接触时就形成回路电流,使内部电路产生光、电信号。该方法与千分表对刀相比较,操作简单,但精度较低。
5.2对刀点为两相互垂直直线的交点
5.2.1采用碰刀方式对刀。对于精度要求不高的加工,可以采用加工时所使用的刀具直接进行碰刀对刀,该方法比较实用,但由于其产生碰刀就会在工件表面留下痕迹,进而影响到对刀精度。为避免损伤工件表面,可以在刀具和工件之间加入塞尺进行对刀,在编程计算时就应将塞尺的厚度减去。
5.2.2机外对刀仪对刀。机外对刀仪是用来测量刀具的长度、直径和刀具形状、角度的专业工具。用机外对刀仪还可测量刀具切削刃的角度和形状等参数,有利于提高加工质量。在使用对刀仪时应注意以下问题:
(1)使用前要用标准对刀心轴进行校准,每次使用前要对Z轴和X轴尺寸进行校准和标定;(2)静态测量的刀具尺寸和实际加工出的尺寸之间有一差值,静态测量的刀具尺寸应大于加工后孔的实际尺寸,因此对刀时要考虑一个修正量,一般该修正量依靠操作者的经验预选,一般要偏大0.01~0.05mm。
5.3刀具Z向对刀
Z向对刀一般有两种方法:
5.3.1机上对刀:该方法是采用Z向设定器依次确定每把刀具与工件在机床坐标的相互位置关系。
5.3.2机上对刀配合机外刀具预调,该方法对刀精度和效率高,但投资大。
6、结语
对刀是影响数控铣床加工质量的一项重要环节,在数控铣床对刀前必须做好对刀点和换刀点的确定,进而确定工件坐标系在机床坐标系中位置的基准点。数控铣床的对刀方法有很多种,不同对刀方法有着不同特点,无论采用何种工具对刀,目的都是为了使机床主轴轴线与刀具端面的交点与对刀点重合,提高加工精度,促进机械加工产业的快速发展。